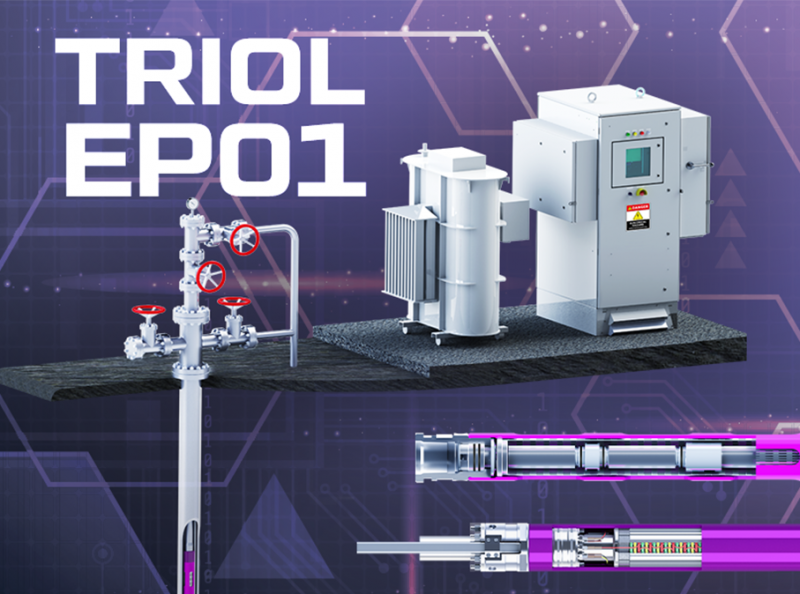
Low flow wells are less efficient than high flow wells because the maintenance cost of such wells for oil companies is not comparable with the profit that the customer receives from these wells.
Cessation of such wells is not profitable, as it will lead to loss of profits received from the high flow wells.
The main challenges in the operation of low flow well fund are related to:
- Energy efficiency.
- Maintenance period.
- Autonomy of equipment operation.
- Redesigning well losses.
- Highly qualified staff.
Currently, the standard production method using ESP has several disadvantages when operating in low flow wells in comparison with ЕР01 technology.
1. ESPs have low efficiency when working in wells with a flow rate of up to 180 bpd. This is because " low efficiency " ESPs up to 180 bpd have low performance, resulting in high energy costs.
The graphs below show that it is possible to compare the efficiency of EP01 compared to ESP in such parameters as efficiency and ROP.
2. Operation of "high-efficiency" ESPs (nominal pump flow rate of 370 bpd) in "Start-Stop" mode leads to the fact that the full potential of the well is not achieved. This is because of a constant change of dynamic level, its decrease during ESP operation, increase - when the pump is switched off, and accumulation process takes place, leads to the point when the average daily flow rate is lower than if the unit operates in constant mode at minimum dynamic mode. The graph below shows how EP01 achieves full well potential.
3. The EP01 units are developed to minimize the energy consumption per barrel of oil produced. The EP01 engine consumes the minimum amount of electric power required to raise the liquid using specialized software. The basis of software operation is that a unique algorithm analyzes motor load at each operation cycle and decides if it is necessary to increase or decrease motor power or decreasing motor operating current. Below is a graph that illustrates how the algorithm works when the well is in operation. The graph shows that the motor current increases as the pressure decreases at the pump intake.
Also below is a comparison in production of EP01 and ESP operating in "Start-Stop" mode
Extension of time between overhaul is provided because EP01 units operate in constant mode compared to ESPs, which operate in "start-stop" mode (more effective mode of ESP operation), there is no accumulation of sand and other mechanical impurities on the working parts of the pump, which can lead to jamming of the pump. The figure below illustrates an ESP guide tube obstructed by mechanical impurities caused by the start/stop mode.
Also, the EP01 unit pump intake is located in the upper part of the pump, resulting in the separation of solids being carried out. Consequently, large-sized particles that can damage the working elements of the pump do not get to the pump's intake. The low flow rate compared to ESP improves solids separation.
![]() |
![]() |
To increase the autonomy of equipment operation in rapidly changing conditions of a low flow well and minimize the time spent by maintenance personnel on the adjustment of equipment operation modes, we offer:
1. Auto-adaptation mode
This mode automatically regulates the number of unit cycles to ensure uninterrupted operation of the equipment without the participation of service staff.
The principle of operation of the algorithm is shown in the diagram below
2. Work optimization by the "Current Regulator" algorithm.
This algorithm adjusts the motor power to ensure uninterrupted operation of the equipment when the intake pressure changes or when an unexpected situation occurs. With this algorithm, the unit operates without stopping and does not require monitoring by service staff.
The graph below shows the automatic changing of the motor current characteristic when the force on the motor rod changes, avoiding breakdowns and consequently reducing the unit's life.
In addition to the above, the software is supplemented by an electronic flow meter.
At this time, optimization of equipment operation is carried out according to the algorithm (cluster mining):
1. Receives data from the external metering device
2. Corrections are made in the equipment operation
3. Within 24 hours, receives data on flow rate.
4. A decision is made about the following changes in operation or continuous operation in this mode
Flowmeter will provide real-time data on the flow rate of the plant and make adjustments to the equipment without waiting for data from an external metering device and save up to two days of commissioning and optimization of the equipment.
Production with EP01 technology reduces conversion losses because high-yield wells are operated with ESP, and after the flow rate drops below 240 bpd, the oil company decides to continue operating with ESP in "Start-Stop" mode or to switch to production using a sucker-rod pumping unit. However, switching to SRP leads to much work to replace the wellhead equipment and prepare the area for installing the pumping unit. The oil company loses at least one day for preparing the wellhead to install the pumping unit.
The oil company loses at least one day for preparing the wellhead and additional staff.
Installation of ЕР01 does not require special equipment or work for wellhead preparation after operating the well with ESP. Similar ESP equipment is appropriate for installation and operation.
Highly qualified staff and a lengthy training process are not required to work with the equipment as:
- The auto-adaptation algorithm and current regulator require minimal settings to start and adjust during maintenance of the equipment, thus reducing the qualification requirements for operating staff.
- The equipment installation system is simplified—no need for responsible and time-consuming operation of oil filling of the motor and hydro-compensator. The motor comes already filled with oil and does not require additional work; the only thing that is required is to connect the motor and pump by screwing seven threaded connections, 6 of which are studs of the flange connection similar ESP and connect the power cable in the head of the
motor. The whole installation process takes no more than 10 minutes. The operations to be performed for the installation of EP01 are given below:
- Simplified commissioning of equipment by:
· Intuitive HMI
- It is not necessary to perform complex calculations and change many settings to start the equipment. To start EP01, it is enough to set well parameters such as temperature, pump lowering depth, target pressure at the pump intake, select in the menu the type of motor and pump you have, length and cable cross-section, transformer parameters, set the dropout, which is already calculated by the software and displayed on the controller screen. It takes 5 minutes even for unqualified staff to put into operation
You can learn more about the installation by following this link